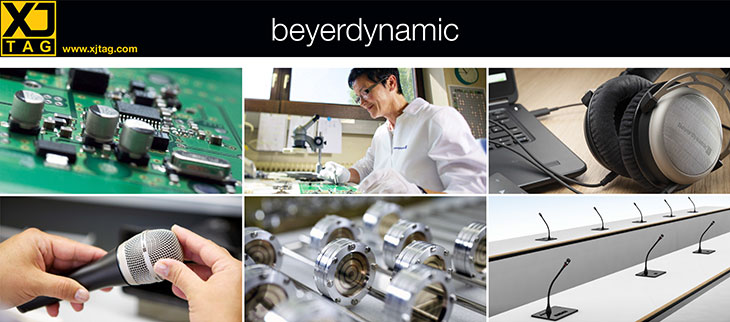
Audio-Conferencing Leader Accelerates Test and Programming with XJTAG Boundary Scan
beyerdynamic, the longest-established brand in the professional audio sector, dating back to 1924, today produces high-end headphones, microphones and conferencing systems. As product complexity increases, high-speed test and programming is essential to keep productivity up and production costs down. The XJTAG boundary scan system helps engineers achieve both these goals.
beyerdynamic creates advanced conferencing systems used in exhibition venues, concert halls, town halls and offices worldwide. It also produces high-performance professional microphones and high-end consumer headphones, which bring the beyerdynamic name to an even wider audience. Products like the Orbis conference system, with more than 13 independent channels, digital sound processing and software-based controls for user comfort, define the current state of the art in mid-range conferencing systems.
As you might expect, beyerdynamic’s sophisticated products contain cutting-edge embedded electronics comprising components like digital signal processors (DSPs), serial flash and high-speed memories, precision converters, and many audio I/O channels and control interfaces.
The company’s engineers have chosen XJTAG Boundary Scan to test these complex assemblies, and to program components like memories, microcontrollers and FPGAs on the board. The flexibility of the system, fast device programming, and helpful features that streamline test creation and fault finding, have made XJTAG a favourite among the technical staff at the Heilbronn headquarters, where most of the products are designed and made.
“As each product generation becomes more highly featured and sophisticated, having a fast and efficient means of programming and testing becomes increasingly important,” says Robert Hertel, FPGA & Communication Systems Design Engineer at beyerdynamic. “Choosing XJTAG to add boundary scan to our test strategy has helped us increase coverage and identify any boards with manufacturing defects much more quickly and easily.”
“Using XJRunner in conjunction with an XJAccelerator board enables us to load application code into SPI Flash up to 90% faster than with an off-the-shelf programmer, by programming at close to the device’s theoretical maximum speed,” he continues. “What’s more, we can easily do the programming from any conveniently available PC due to the simple licensing system that XJTAG uses, whereas moving the dedicated programmer to a different machine is more time-consuming.”
The engineering teams are using XJTAG throughout the entire product development, production and service lifecycle. In the factory, it is integrated with LabVIEW, which enables the engineers to take advantage of XJTAG’s powerful features from within their preferred test executive. But the XJTAG project created for use with LabVIEW is also used standalone, for example for servicing purposes. As Robert Hertel explains, “We can re-use and continuously develop test scripts for different products and various roles, which has enabled us to accelerate prototype development, increase test-engineering productivity, and troubleshoot returned units more quickly and efficiently than before. The automatic Connection Test finds most defects with minimal effort, and features such as XJAnalyser and built-in Layout and Schematic Viewers can quickly identify and locate the causes of failures during the test.”
The technical support delivered by engineers at XJTAG’s Cambridge, UK, headquarters, completes the picture. Robert Hertel sums up, “Getting timely answers is very important for us to keep our projects and production on schedule, and XJTAG’s engineers always respond quickly, often adding suggestions to further increase testability of our boards. Overall, XJTAG has proved to be a reliable partner, a great value and a highly effective solution to our needs.”
Choosing XJTAG to add boundary scan to our test strategy has helped us increase coverage and identify any boards with manufacturing defects much more quickly and easily.
Using XJRunner in conjunction with an XJAccelerator board enables us to load application code into SPI Flash up to 90% faster than with an off-the-shelf programmer, by programming at close to the device’s theoretical maximum speed. What’s more, we can easily do the programming from any conveniently available PC.
Getting timely answers is very important for us to keep our projects and production on schedule, and XJTAG’s engineers always respond quickly, often adding suggestions to further increase testability.
Company:
beyerdynamic GmbH & Co. KG
HQ Germany
Nature of business: World leading designer and manufacturer of professional audio products
Main products:
Headphones, microphones and conference systems
Customers:
Serving the Broadcast, Music, Tele / Video Conferencing, Recording / Film / Studio / Live, and High-end Consumer markets
Founded: 1924 in Berlin
Employees: 370
Revenues: € 50 million
Location: Heilbronn, Germany
Web site: www.beyerdynamic.com