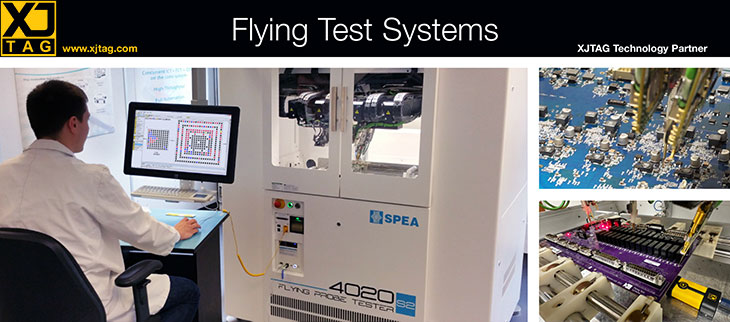
Test Experts Select XJTAG as Best Boundary Scan System
Flying Test Systems Ltd (FTSL), a specialist in PCBA test solutions, benchmarked three boundary scan systems when it became unhappy with the one it had used for several years. The comparison revealed one clear winner, and their engineers switched to using XJTAG. FTSL now integrates XJTAG boundary scan into many of its test solutions.
FTSL offers a variety of services to the electronics industry and works across almost all sectors including automotive, military, space, aerospace, aviation, medical, and industrial. For those clients who need a full working system to be delivered, FTSL’s engineers develop the complete solution. That can include the creation of programs for flying probe testers with integrated boundary scan functionality, or the development of bed-of-nails systems. For customers with existing functional testers, FTSL helps them improve efficiency by integrating boundary scan into their systems; and for clients who don’t have access to test facilities, FTSL offers to create the test programs and to test their assembled boards for them.
FTSL decided to benchmark different boundary scan test systems after it became unhappy with how slowly support requests were being resolved for its existing boundary scan solution. One key item in their comparison was how long it took to create a working test project, and the results were clear: with the XJTAG system, the project was running after just half a day whereas solutions from other providers took up to three days. “From a business perspective, that made XJTAG an obvious choice,” said Nigel Priest, FTSL’s Managing Director: development time is very important to his busy company and to its clients.
The other advantages of XJTAG also quickly became apparent. For example, they discovered how effectively it maximised test coverage across the board. Priest said, “What it delivered straight out of the box was quite incredible in terms of the depth of coverage.”
FTSL’s engineers also found how easy the XJTAG system is to use, especially with its user-friendly graphical interface. Cheryl Rogers, FTSL’s Commercial Director, commented, “Our engineers who do the boundary scan work love the XJTAG system. It’s so much easier.”
Depending on the client’s needs, the tests that FTSL develop may be executed from XJRunner’s GUI, or integrated into a system built using National Instruments™ LabVIEW™.
“Another advantage is the ability to program at full speed,” Priest said. FTSL uses both XJFlash (which utilises the board’s FPGA as a vehicle for ultra-fast memory programming) and XJDirect (which is used when memory is connected to a microprocessor).
Priest concluded, “The XJTAG tools and the interface are clearly best in class.”
And when FTSL’s engineers needed advice, they found XJTAG support was the best. Rogers said, “With other boundary scan providers, we found it was exceedingly difficult to get help, but if we have an issue now, we can ring XJTAG and our query is resolved very swiftly. For us, that’s a really critical factor.”
FTSL also partners with ICT equipment manufacturer SPEA, and often uses a SPEA-XJTAG integration to add XJTAG boundary scan to flying probe systems. The combination allows more of the board to be tested because boundary scan can apply a stimulus that is then monitored farther into the circuit by a probe, and vice-versa. Priest said, “Our customers love that this allows us to test as much as possible in a single stage early in the manufacturing process. On one board we had, 25% of it couldn’t have been tested without adding boundary scan.”
The XJTAG tools and the interface are clearly best in class.
On one board we had, 25% of it couldn’t have been tested without adding boundary scan.
Our engineers who do the boundary scan work love the XJTAG system. It’s so much easier.
Company: Flying Test Systems Limited
Nature of business: Leading UK provider of electronic test solutions
Main products: SPEA flying probe and bed-of-nails testers, boundary scan and functional test solutions
Customers: Electronics companies in almost all industry sectors
Established: 2004
Location: Saunderton, near High Wycombe, UK
Web site: www.flyingtest.co.uk