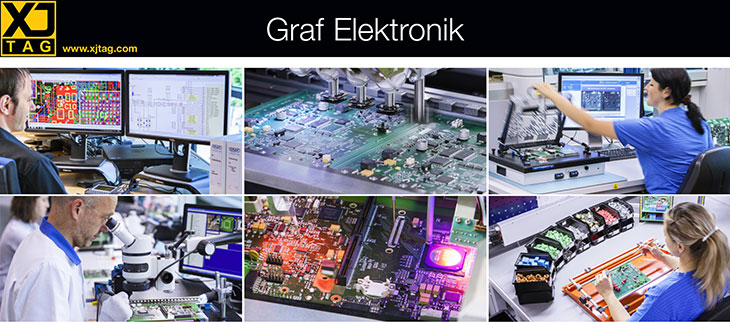
Austrian manufacturing experts rate XJTAG as top boundary scan system
Graf Elektronik, an Electronic Manufacturing Services provider in the Lake Constance region joining Switzerland, Germany and Austria, worked with a client to identify the best boundary scan test platform to achieve mutual objectives. The evaluation rated XJTAG as number one for user friendliness, features and value for money.
Graf Elektronik specialises in electronics development and electronics manufacturing services, and has clients across the industrial, medical, and consumer-products sectors. Its service portfolio includes project management, hardware development, software development, mechanical design, circuit-board assembly, test engineering and production-line testing, painting, potting, and box-build ready for sale.
Recently, the company’s engineers worked with a client that serves the electrical power industry with innovative products and services for testing, diagnostics and monitoring of protection circuits. The objectives were to increase test coverage and raise productivity when building the client’s power-testing equipment, augmenting Automatic Optical Inspection (AOI) and In-Circuit Testing (ICT) with JTAG boundary scan testing.
During the evaluation, engineers from Graf Elektronik and the client company carefully compared the support, software, hardware, functionality, and the cost of boundary scan systems from several well-known vendors. This rigorous comparison examined both the development and run-time environments of the leading platforms, as the two partners intended to use both environments to develop and execute tests.
“XJTAG was by far the most user-friendly of the systems we evaluated, yet its superior ease of use did not come at the expense of features”, says Marcél Ströhle, Testing Coordinator, Graf Elektronik. “We found XJTAG to have the most intuitive workflow while offering a very competitive price. XJTAG also gives us the ability to rapidly develop and deploy new tests.”
Graf Elektronik is also supplying their client with the boundary scan tests originally developed for use in production. This way the company can use XJTAG’s XJRunner run-time environment in-house to speed up analysis of any returned units.
Marcél Ströhle and the engineering team at Graf Elektronik are using XJTAG to check bus interfaces between various chips, DSPs, FPGAs and other complex ICs. “The ability to test DDR2 and DDR3 RAM connections without functional testing is incredibly helpful, and checking connectors through external boards significantly increases our typical test coverage of digital circuits”, he explains.
He highlights XJTAG tools like the Layout Viewer and XJAnalyser as being especially powerful. Layout Viewer helps the user find the physical location of components, nets and pins on a board, and to visualise any faults that are found when running tests. XJAnalyser enables the user to set pin values and trace signals, and so debug boards quickly. It can also be used to program devices, thereby saving expenditure on other download tools.
Marcél Ströhle goes on to explain how XJTAG also helps engineers identify unusual defects that are invisible to AOI and cannot be pinpointed using ICT. “We successfully created custom tests that enabled us to trace some unexpected faults back to a bad batch of ICs,” he adds. “Developing new tests is very easy, since the user interface is more intuitive than the other systems we evaluated, and a lot of pre-packaged tests are available online to help us get powerful tests up and running quickly.”
XJTAG was by far the most user-friendly of the systems we evaluated, yet its superior ease of use did not come at the expense of features.
The ability to test DDR2 and DDR3 RAM connections without functional testing is incredibly helpful, and checking connectors through external boards significantly increases our typical test coverage of digital circuits.
Developing new tests is very easy, since the user interface is more intuitive than the other systems we evaluated, and a lot of pre-packaged tests are available online to help us get powerful tests up and running quickly.
Company: Graf Elektronik GmbH
(Part of Graf Group, Austria)
Nature of business: One of the leading Electronics Manufacturing Services providers for OEMs in Austria
Main product: Full service from development to testing and volume production of certified electronic assemblies and devices
Location: Dornbirn, Austria
Incorporated: 1989
Employees: 135
Revenues: €20 million (2013)
Web site: www.grafgroup.com