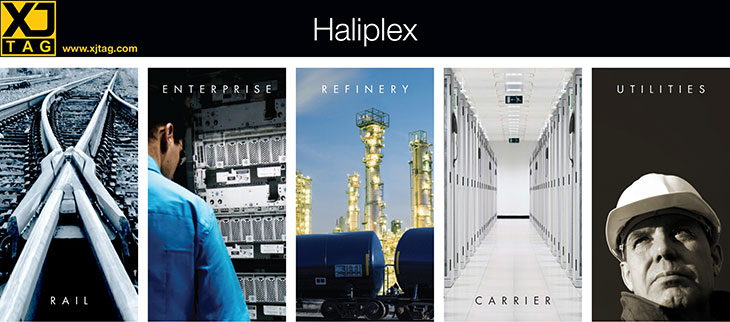
Haliplex cuts costs, waste and time to market using XJTAG Boundary Scan
Australian communication equipment producer Haliplex is saving over US$100,000 a year through time savings and reduced waste, by taking advantage of XJTAG’s convenient features supporting fast, confident test development as well as advanced capabilities to identify faults well beyond the boundary scan chain.
Haliplex Pty Ltd, based near Melbourne, Australia, produces multi-service voice and data equipment for network-edge applications with enterprises such as transport operators, utilities and telecom carriers. Serving both domestic and export markets, the company prides itself on delivering products that are the smallest of their kind and can be deployed in flexible ways within existing or new networks supporting high-bandwidth standards such as Gigabit Ethernet and SDH/SONET.
Products such as the Haliplex HPX1600 series of multi-service access terminals contain PCBs that are densely populated with devices such as high-performance embedded processors, FPGAs and ASICs, as well as high-speed telecom data-path devices. Other components include optical fibre drivers, I2C and SPI devices, and Ethernet switches. By using XJTAG boundary scan to debug prototypes and to test production units, Haliplex calculates it is saving over US$100,000 every year.
Anthony Merry, Chief Technical Officer at Haliplex, explains. “XJTAG allows us to achieve high test coverage for each board, and helps trace faults accurately to save debugging and repair time. This has reduced the typical time to commission a new design for production by around four days. Given the number of new boards we develop in a year, for example, this saves us around US$24,000 of engineers’ time. This alone means that XJTAG pays for itself extremely quickly. But we are gaining further savings by also basing our production test strategy on XJTAG.”
The boards are built by a manufacturing partner, which uses the XJRunner run-time-only version of XJTAG optimised for production-test applications, to test each production unit. Device programming and loading of serial numbers is also completed from within the boundary scan environment.
“XJRunner has diagnostic features that help our manufacturer track down faults that would otherwise consign a proportion of boards to our ‘repair pile’. This has reduced the number of failed boards passed to us by around 90%, saving over US$64,000 of waste per year as well as around US$12,000 of our repair technicians’ time”, says Merry.
He explains that the high test coverage achievable, and the extra confidence XJTAG gives to engineers when developing tests are key factors contributing to these financial savings. “XJTAG’s graphical environment and high-level test language enable our engineers to create tests for specific functions or areas of the board quickly and accurately. Other systems tend to hide details, which makes it difficult to be sure that certain aspects are covered.”
“We can also test non-JTAG devices well beyond the boundary scan chain from within XJTAG, which helps boost productivity and quality”, he continues. As well as providing convenient features such as automatic testability analysis, XJTAG is able to use board-level interconnects such as I2C or SPI to reach non-JTAG devices not directly connected to those on the boundary scan chain. This allows engineers to achieve high test coverage using boundary scan, when testing boards containing components such as ADCs, DACs, serial memories, sensors, display drivers or switches.
“XJTAG combines powerful capabilities with an extremely competitive price, and represents outstanding value among boundary scan test systems.”
XJTAG saves us over US$100,000 per year by reducing the engineering time to commission new boards, enabling us to repair boards more quickly, and reducing the number of boards that are scrapped.
Its graphical environment and high-level test language enable our engineers to create tests for specific functions or areas of the board, quickly and accurately. Other systems tend to hide details, which makes it difficult to be sure that certain aspects are covered. XJTAG combines powerful capabilities with an extremely competitive price, and represents outstanding value among boundary scan test systems.
Company: Haliplex Pty Ltd
HQ Australia
Nature of business:
Leading manufacturer of next-generation edge access and multiplexing solutions
Main products: HPX-800, HPX-1600
Customers:
Progressive Utility, Telecoms and Transport operators such as Nokia Siemens Networks, KAMO Power, Fibrerail Malaysia, KTM Berhad, BC Hydro, Bayly Communications…
Location: Melbourne, Australia; Sales offices in Australia, USA
Web site: www.haliplex.com