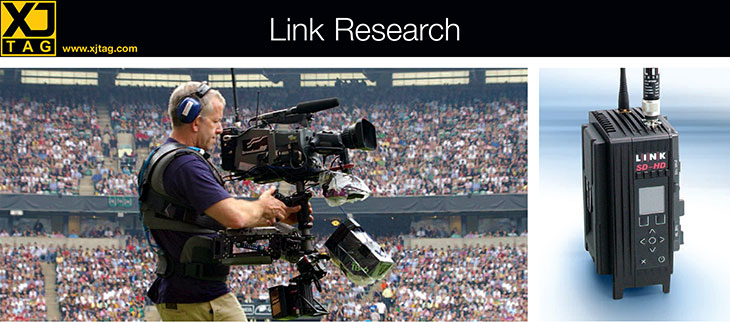
Link Research teams with XJTAG developer and RF specialist Briton EMS to speed wireless camera system manufacture
Link Research, an award winning developer of wireless camera systems, has partnered with Briton EMS, a UK contract electronics manufacture with RF capability and boundary scan test expertise (the company is an approved XJTAG EMS Developer), to speed manufacture of its market-leading range of wireless camera systems, which includes the Link HD and L1500 SD/HD wireless camera transmitters.
Link Research has a reputation for technical innovation and its range of Standard Definition (SD) and High Definition (HD) wireless camera systems are used by major broadcasters throughout the world. For example, Link’s HD wireless camera systems were used at every major venue at the Beijing Olympics, from the fantastic Bird’s Nest Stadium to the Water Cube aquatics centre, to help bring the spectacle to a worldwide audience.
Link Research is part of the Visilink group and has won many awards for its wireless camera technology which uses DVB-T combined with Link’s own LMS-T modulation to enhance the performance of wireless cameras in all kinds of operating conditions and environments. Link’s wireless camera systems are at the cutting edge of wireless camera technology and utilise the company’s own video compression and encoding technology.
To maintain its market leading position, Link Research decided early on to partner with Briton EMS, an experienced electronics manufacturing services (EMS) provider, to enable it to focus its resources on the all-important research and product development activity. One third of Link’s staff are dedicated to developing new products and technologies and the company has a highly talented team of RF (radio frequency) design engineers. The company’s R&D centre is located in Watford, England and it also has offices in Dubai and Singapore.
“We needed a strategic EMS partner that had experience with manufacturing high-end and complex RF products and that was willing to invest in the skills and equipment to support our evolving product plans”, said John Mulcahy, managing director, Link Research. “We also wanted a local supplier that was prepared to work hard alongside our own RF engineers to offer test solutions and manufacturing expertise and to ensure that we continued to improve on product quality, reliability and time to market.”
Bedford-based Briton EMS works in partnership with original equipment manufacturers (OEMs) across different markets including broadcasting, industrial, instrumentation, medical and telecoms. With 22,000 square feet of factory space, the company offers a broad range of services from printed circuit assembly through to complete product build, providing surface mount as well as conventional through-hole assembly.
The company specialises in low and medium volume, high-mix production and also offers electronic and mechanical design services (hardware and software), prototyping, new product introductions (NPI), fulfilment and after-market services.
“We started working with Briton EMS back in 2001 because they had a track record in the broadcast market and offered the full range of product lifecycle services including prototyping, design for manufacture and test, material procurement, PCB and system assembly”, added Richard Lincoln, chief engineer, Link Research. “Also, they were prepared right from the outset to build up their own internal RF test capability to further support our RF design team and to speed up the whole NPI process.”
Tony Abri, commercial director at Briton EMS, said: “We took on board Link’s suggestions about us strengthening our wireless skills and we have since built a very capable team of RF test engineers. We have also invested in a new precision surface mount line to boost productivity and we are constantly improving our test and test development capabilities. This included our investment in boundary scan technology, which is a pre-requisite for any EMS provider working in high end markets”.
Briton EMS selected the XJTAG boundary scan system to overcome the challenges of testing tightly-packed printed circuit boards populated with a growing number of ball grid array (BGA) devices. The company is now a certified XJTAG EMS Developer which means that is using the full development capability of the XJTAG system for debugging, testing and programming complex PCBs and systems throughout the product lifecycle.
“The XJTAG system has transformed our test regime and has enabled us to go far beyond quickly pinpointing faults on complex boards”, said Conor Hogan, test team leader at Briton EMS. “We are now using the system right at the very beginning of the design process as a combined design-debugging and DFT environment.”
Such is the power of the XJTAG system that the Bedford-based company now encourages its customers to populate their boards with JTAG devices, where available, and to ensure that devices are tracked on the board so that they can be accessed via the JTAG boundary scan chain.
“Link Research looks to us as its test development and manufacturing partner and therefore engages with our team very early in the product development cycle sending us the proposed board layout and the corresponding bill of material (BOM) listing as soon as they have it”, added Conor Hogan. “This enables us to decide right away what kind of test is required.”
“Our relationship with Link Research’s R&D team is such that if we make a suggestion to add circuitry to a board, for example”, continued Hogan, “they will generally co-operate if it means extending the test coverage, particularly as this normally speeds up the whole development process and increases production output.”
Since using the XJTAG system, Briton EMS has been able to shorten the development cycle and increases the yield on many of the high complexity products that it manufactures. The company does lots of NPI work – around 130 products each year or almost three per week – and having a powerful tool that can be used throughout the design, prototyping, production and post-production stages is a major advantage.
In the case of Link Research, the company’s latest double-sided surface mount boards, for example, contain multiple 1152-pin field programmable gate arrays (FPGAs), along with DSPs, memory devices, other high speed processors, LEDs, communication devices and a power supply.
“Using XJTAG, we are achieving 92% test coverage on the complex boards that are used in Link’s HD Wireless camera transmitter”, added Conor Hogan. “We run the connection tests and debug the board using XJTAG before loading Link’s firmware in the DSP as this saves a lot of time.”
Working in high end technology markets, such as the wireless RF sector, it’s vital for suppliers, whether contract manufacturers or their test partners, to continuously enhance their capabilities to respond to a customer’s evolving needs.
“For a customer such as Link Research, the wireless transmitters we manufacture must produce a robust and stable RF signal that is accurate to 1Hz and doesn’t interfere with other devices”, added Conor Hogan. “To achieve this, and to constantly improve quality and output whilst reducing cost, we need the very latest equipment and all the skills and ingenuity of our engineering and manufacturing teams.”
Furthermore, just as Link Research relies on its strategic EMS provider, Briton EMS in turn looks to its partnerships with suppliers such as XJTAG to help it solve complex test issues.
“XJTAG’s technical support is exemplary and they work in partnership with us to overcome problems”, added Conor Hogan. “For example, we had an issue recently with trying to test two of Link Research’s boards that fit together with multi-way connectors but we couldn’t sync the PCBs. We called XJTAG, they came and took the boards away and within a day or so resolved the timing differences between boards by using their add-on XJIO board. That’s the kind of added value that we look for from our partners and that’s what differentiates XJTAG from the rest of the market!”
We needed a strategic EMS partner that had experience with manufacturing high-end and complex RF (radio frequency) products and that was willing to invest in the skills and equipment to support our evolving product plans. We also wanted a local supplier that was prepared to work hard alongside our own highly talented RF engineers to offer design for test and manufacturing expertise and to ensure that we continued to improve on product quality, reliability and time to market.
Company: Link Research
(part of the Visilink group)
Nature of business: Wireless camera system manufacturer
Main products: Link’s L1500 wireless camera transmitter works in Standard Definition and High Definition
Customers: Major broadcasters throughout the world
Locations: Locations in Watford (England), Singapore and Dubai (UAE)
Revenues: £15m
Web site: www.linkres.co.uk