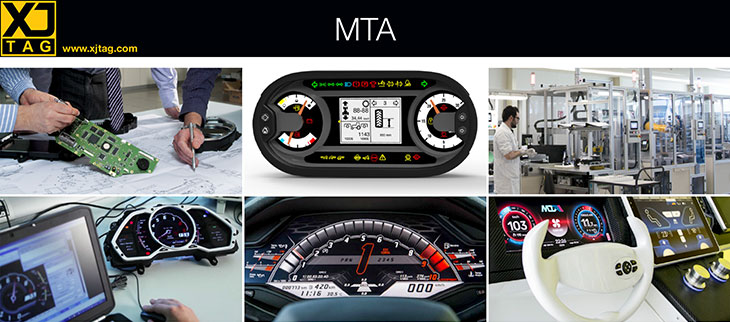
Automotive Innovator Accelerates Test and Programming with XJTAG Boundary Scan
MTA S.p.A in Italy creates advanced instrumentation for all types of vehicles, hosted on sophisticated embedded systems built and tested in-house. Seeking to enhance quality and efficiency by using boundary scan for testing and programming, MTA chose XJTAG for its powerful development environment and outstanding technical backup.
In the world of advanced automotive electronics, where quality and safety are of paramount importance, MTA S.p.A is a leader in innovative instrumentation for cars, motorcycles, trucks, and buses. As customers expect increasingly smart, dynamic and colourful user experiences, uncompromising clarity, and ease of use, with outstanding safety, quality and value for money, MTA’s dashboards and infotainment centres are based on sophisticated and flexible embedded systems comprising advanced processors, high-speed memories, and state-of-the-art communication interfaces.
Manufacturing its products in-house, the company needs powerful test facilities to provide the highest quality assurance and maximise production throughput. Continually striving to improve, MTA’s test engineers have chosen to introduce boundary scan to their product development and production test activities. They have invested in the XJTAG Development System to create and run tests, and, for production, are using the specialised run-time environment, XJRunner, to integrate with and augment the capabilities provided by a SPEA In-Circuit Test system. This extends test coverage to components in packages such as BGA or CSP that have inaccessible I/O pins. Increasingly, components like memories, FPGAs and processors rely on these types of packages to meet demands for large numbers of I/O pins within a small PCB footprint.
Alberto Neri, Test Manager at MTA, explains how his team selected XJTAG. “We evaluated the major boundary scan systems, and chose XJTAG for its superior features and support,” he says, adding, “The development environment is powerful and easy to understand, with a clear and intuitive user interface. Given our line of business, it’s no surprise that clarity and ease of use are high on our list of priorities.”
In addition to the quality of the user interface, he also highlights the support from XJTAG headquarters in Cambridge as a key factor influencing the decision. “XJTAG’s engineers answer all our questions quickly and efficiently, which has made our learning curve even faster and smoother. Moreover, we have continued to enjoy great backup, including free access to XJTAG’s large library of device tests, and expert help with writing custom test scripts when needed. In addition, the XJTAG system automates tests such as connectivity, pull-resistor and logic tests and provides tests for thousands of device types such as memory. The XJTAG system also performs Design for Test (DFT) analysis to help further increase coverage and also allow test optimisation to reduce overall test cycle times.”
MTA is not only using XJTAG to boost in-circuit test, but is also using XJRunner to program devices like CPLDs, flash memories, and microcontrollers. Programming speed can be further improved with optional applications like XJFlash, which can program flash at close to its theoretical maximum speed.
By eliminating the need to program devices separately, XJTAG’s ability to program devices on the board, inline, helps streamline product assembly and raise efficiency and throughput. Alberto Neri concurs, “XJRunner has been integrated with our PC-based test software, developed with NI LabVIEW, and the combination allows us to work efficiently in our own familiar environment.”
“Test and in-system programming are faster and more efficient with XJTAG,” he concludes.
We evaluated the major boundary scan systems, and chose XJTAG for its superior features and support.
The development environment is powerful and easy to understand, with a clear and intuitive user interface. XJRunner has been integrated with our PC-based test software, developed with NI LabVIEW.
XJTAG’s engineers answer all our questions quickly and efficiently, which has made our learning curve fast and smooth. Moreover, we have continued to enjoy great backup, including free access to XJTAG’s large library of device tests, and expert help with writing custom test scripts when needed.
Company: MTA S.p.A.
Nature of business:
Global leading designer, developer and manufacturer of automotive electronic and electromechanical components
Main products:
In-vehicle HMI (Human Machine Interface) systems & control panels
Customers:
World’s leading car, motorcycle, truck and tractor manufacturers
Founded: 1954
Employees: 1,300
Locations:
Two plants in Italy (Codogno and Rolo) and 8 sites worldwide
Web site: www.mta.it