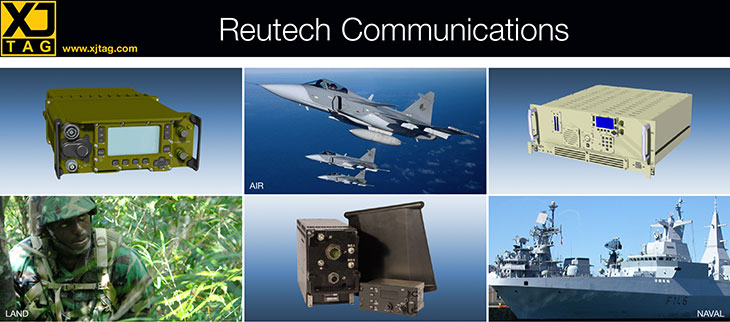
Software-defined radio innovator enhances test regime with XJTAG boundary scan
Tactical radio specialist Reutech Communications identified boundary scan as the best way to streamline device programming and increase test coverage for boards with large numbers of inaccessible I/Os. Choosing XJTAG delivered additional advantages including in-built support for board-level traceability and a unified test and programming environment spanning development and production.
Reutech Communications Pty Ltd, based in Pinetown, South Africa, is a specialist developer and producer of tactical V/UHF transceivers for airborne, shipborne and land environments. Supplying the South African National Defence Force and export markets, the company’s latest-generation products are software-defined radios for secure tactical voice and data communications.
The radios are hosted on a high-performance, flexible hardware platform providing the processing resources for frequency hopping, encryption, data networking and state of the art modulation techniques. Major components include DSPs, FPGAs, Flash chips and RAM, typically in BGA or chip-scale packages featuring area-array interconnects. Since these cannot be tested using ordinary probes, Reutech’s engineers needed a way of testing without accessing the device I/Os.
“Complex, mission-critical boards cannot be tested adequately using one approach alone. We apply a number of techniques beginning with in-circuit test and finally testing assembled radio modules using purpose-built Automated Test Equipment”, explains test engineer José Bastos. “With the large numbers of BGAs and SMD devices now used on our boards, we have seen the need to extend our test regime further to achieve the high level of coverage we require.”
By using XJTAG boundary scan, Reutech is now able to increase test coverage for production boards, and is gaining additional benefits as a result of the system’s flexibility and unique enhanced features.
“With boundary scan, test coverage is not dependent on I/O accessibility, and devices can be programmed in situ to help streamline production and test procedures. When making our choice of test system we also looked for a high standard of test reporting, to support accurate traceability. This is a pre-requisite in the sectors we serve. The quality of the user environment was also important to us.”
José Bastos and the team chose XJTAG after comparing a number of systems. In addition to achieving a convenient, unified platform enabling increased test coverage, in-system programming and board-level traceability, choosing XJTAG promised further productivity advantages by tightly integrating board design, prototype debugging and production test.
“The XJTAG graphical environment is easy to use, and allows us to monitor, drive, pin-toggle, debug and program devices quickly and easily. Moreover, the XJEase high-level language allows tests to be written during development, and then stored to be used in production,” confirms José Bastos. “One particularly powerful aspect of the system is the ability to write tests at the device level, which allows us to respond quickly to board design changes and to re-use a test in any future project using the same device.”
Production boards are built externally and are returned for testing and final assembly. “We test the assembled PCBs using ICT and boundary scan, and rework any failed boards before they are functionally tested and integrated into the product. Choosing XJTAG has proved highly successful; it has enabled us to reach the high level of test coverage we require while also helping achieve our productivity and traceability goals.”
The XJTAG graphical environment is easy to use, and allows us to monitor, drive, pin-toggle, debug and program devices quickly and easily. The XJEase high-level language allows tests to be written quickly at the device level, which enables us to respond quickly to board design changes and to re-use a test in any future project using the same device.
Choosing XJTAG has proved highly successful; it has enabled us to reach the high level of test coverage we require while also helping us achieve our productivity and traceability goals.
Company: Reutech Communications Pty Ltd.; HQ South Africa
Nature of business: South Africa’s leading supplier of military radios
Main product: Development, industrialisation and production of tactical V/UHF transceivers for the airborne, shipborne and land environments
Customers: South African National Defence Force, as well as export market
Location: Pinetown, South Africa
Employees: 140 end 2009
Revenue: US$ 15 million in 2009
Web site: www.reutechcomms.co.za