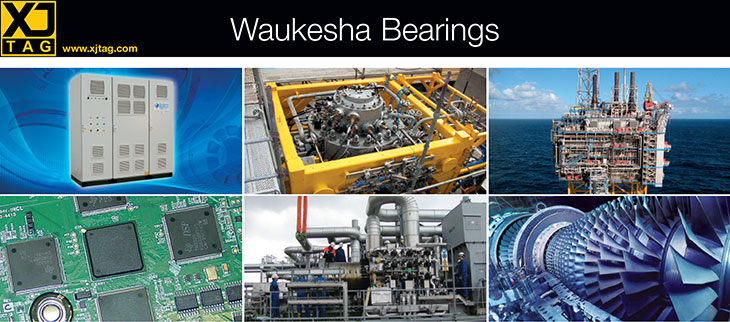
Leader in magnetic bearings streamlines innovation with XJTAG boundary scan
Waukesha Magnetic Bearings, based in Worthing, UK, is using XJTAG to perform boundary scan testing of high-speed real-time digital control boards for its active magnetic bearings. The XJTAG system is in action throughout development and production, speeding up prototyping, saving board re-spins, and helping dramatically reduce production test duration.
Waukesha Magnetic Bearings™ (WMB) leads the industry in custom-engineered magnetic bearing systems for large turbomachinery and high-performing rotating equipment in oil & gas, power generation and defence markets. WMB’s hardware designs allow direct immersion in the process fluid often eliminating shaft seals, while the control software provides for automatic tuning, remote monitoring and diagnostics thus reducing operating costs while maintaining near perfect availability. WMB is a Waukesha Bearings Business under the Energy segment of Dover Corporation.
Engineers designing the next generations of digital controllers at WMB’s UK technical centre in Worthing, have chosen the XJTAG boundary scan system to help verify new designs, test prototypes quickly, and apply boundary scan tests to production boards.
The XJTAG system quickly gained respect in the development laboratory by helping engineers pinpoint two incorrect connections on the first prototype of a new controller board. These could have taken hours to locate using conventional test techniques, according to Colin Pennifold, Electronics Technician at WMB. “XJTAG saved at least one re-spin of our new printed circuit board (PCB) design”, comments Electronics Design Engineer, Steve Dabbs. “The system is easy to use, with time-saving features such as the Advanced Connection Test and ready-to-run scripts for testing many types of memory ICs. We can also test BGA devices, which are almost impossible to test using other means.”
XJTAG provides clear reports with clickable links to graphical viewers that guide the user to the detected fault location. These graphical tools include the Layout Viewer and Schematic Viewer, which are featured in both the XJDeveloper application and XJRunner production-test system. The Layout Viewer helps quickly pinpoint faults on the board by highlighting selected components and nets, and allows individual PCB layers to be displayed or hidden for clarity. Schematic Viewer displays the logical arrangement of circuit elements to show how a device is being used in the circuit, and enables faster testing by highlighting areas of interest without requiring the user to continually change applications.
WMB is also using boundary scan as part of the test regime for its production boards, and has integrated the XJRunner system into custom test stations that perform stand-alone testing of the PCBs. XJRunner provided the flexibility for the test engineering department to design and build test fixtures using a CPLD to connect to the PCB under test.
“It was important to have the freedom to create this test fixture, which we are using to test connections and signal paths within the PCB and connections to or from sockets on the PCB”, confirms Steve Dabbs. “By adding XJRunner to our production test capability, we have been able to significantly increase test coverage while also achieving substantial time savings over manual testing. In fact, the total test duration has been reduced from around 7.5 hours per board to under two hours.
“Overall, XJTAG boundary scan has delivered a great return on our investment.”
XJTAG saved at least one re-spin of our new PCB design. The system is easy to use, with time-saving features such as the Advanced Connection Test and ready-to-run scripts for testing many types of memory ICs. We can also test BGA devices.
By adding XJRunner to our production test capability, we have been able to significantly increase test coverage while achieving substantial time savings over manual testing. In fact, the total test duration has been reduced from around 7.5 hours per board to under two hours.
Overall, XJTAG boundary scan has delivered a great return on our investment
Company: Waukesha Bearings Corporation, HQ USA
Nature of business: Leading designer / manufacturer of engineered hydrodynamic bearings and magnetic bearing systems
Main product: Custom bearing systems for large turbomachinery and high-performing rotating equipment
Customers: The world’s leading OEMs and end-users in oil & gas, power generation, marine/defense and industrial markets
Location: Offices and plants in the USA, UK, Russia; Representatives worldwide
Web site: www.waukbearing.com